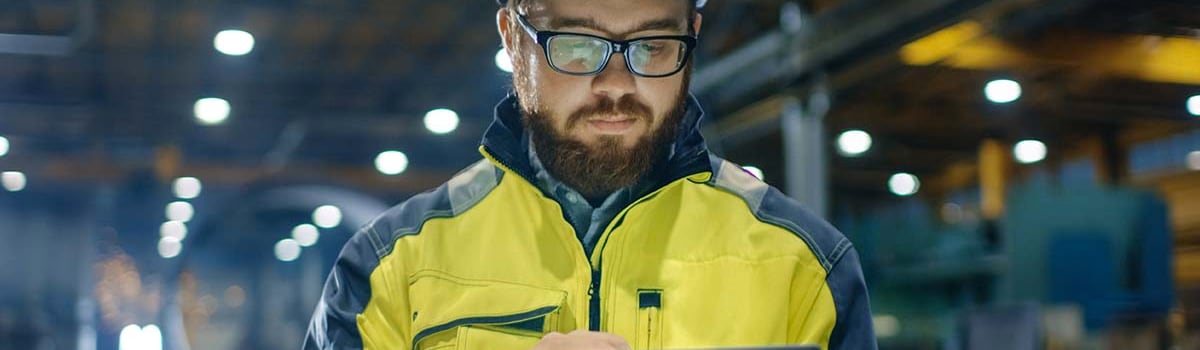
{"storeInfo":{"id":13,"name":"Power Equipment Direct","domain":"powerequipmentdirect.com","initials":"PED","url":"https:\/\/www.powerequipmentdirect.com","path":"\/var\/www\/vhosts\/ped.com\/"},"headerNavJSON":"{\"MainLinks\":[{\"URL\":\"\\\/outdoor\\\/air-compressors-direct.html\",\"displayText\":\"Air Compressors\",\"sectionLinks\":{\"columns\":\"6\",\"linkItems\":[{\"URL\":\"\\\/tools\\\/portable-air-compressors.html\",\"imageURL\":\"\\\/nav-image\\\/100\\\/compressor-13-1.jpg\",\"displayText\":\"Portable\"},{\"URL\":\"\\\/tools\\\/gas-air-compressors.html\",\"imageURL\":\"\\\/nav-image\\\/100\\\/compressor-13-2.jpg\",\"displayText\":\"Gas\"},{\"URL\":\"\\\/tools\\\/single-stage-air-compressors.html\",\"imageURL\":\"\\\/nav-image\\\/100\\\/compressor-13-3.jpg\",\"displayText\":\"Single-Stage\"},{\"URL\":\"\\\/tools\\\/two-stage-air-compressors.html\",\"imageURL\":\"\\\/nav-image\\\/100\\\/compressor-13-4.jpg\",\"displayText\":\"Two-Stage\"},{\"URL\":\"\\\/tools\\\/rotary-screw-air-compressors.html\",\"imageURL\":\"\\\/nav-image\\\/100\\\/compressor-13-5.jpg\",\"displayText\":\"Rotary Screw\"},{\"URL\":\"\\\/tools\\\/scroll-compressors.html\",\"imageURL\":\"\\\/nav-image\\\/100\\\/compressor-13-6.jpg\",\"displayText\":\"Scroll\"}]},\"subCategories\":[{\"URL\":null,\"type\":\"list\",\"title\":\"Featured Categories\",\"linkItems\":[{\"URL\":\"\\\/tools\\\/wheelbarrow-air-compressors.html\",\"displayText\":\"Wheelbarrow\"},{\"URL\":\"\\\/tools\\\/air-dryers.html\",\"displayText\":\"Air Dryers\"},{\"URL\":\"\\\/tools\\\/truck-mount-air-compressors.html\",\"displayText\":\"Truck Mount\"},{\"URL\":\"\\\/tools\\\/twin-stack-air-compressors.html\",\"displayText\":\"Twin Stack\"},{\"URL\":\"\\\/oil-free-air-compressors.html\",\"displayText\":\"Oil Free\"}]},{\"URL\":null,\"type\":\"list\",\"title\":\"Accessories\",\"linkItems\":[{\"URL\":\"\\\/tools\\\/impact-wrenches-pneumatic.html\",\"displayText\":\"Impact Wrenches\"},{\"URL\":\"\\\/tools\\\/air-treatment.html\",\"displayText\":\"Air Treatment\"},{\"URL\":\"\\\/tools\\\/air-tools.html\",\"displayText\":\"Air Tools\"},{\"URL\":\"\\\/tools\\\/air-compressor-accessories.html\",\"displayText\":\"All Accessories\"},{\"URL\":\"\\\/tools\\\/line-filters.html\",\"displayText\":\"Line Filters\"}]},{\"URL\":null,\"type\":\"list\",\"title\":\"Shop by Brand\",\"linkItems\":[{\"URL\":\"\\\/tools\\\/ingersoll-rand-air-compressors.html\",\"displayText\":\"Ingersoll Rand\"},{\"URL\":\"\\\/tools\\\/quincy-air-compressors.html\",\"displayText\":\"Quincy\"},{\"URL\":\"\\\/tools\\\/atlas-copco-compressors.html\",\"displayText\":\"Atlas Copco\"},{\"URL\":\"\\\/tools\\\/emax-air-compressors.html\",\"displayText\":\"EMAX\"},{\"URL\":\"\\\/tools\\\/industrial-air-compressors.html\",\"displayText\":\"Industrial Air\"}]},{\"URL\":\"\\\/stories\\\/156-How-to-Pick-the-Perfect-Air-Compressor.html\",\"type\":\"image\",\"title\":\"Buyer's Guide\",\"imageURL\":\"\\\/nav-article-image\\\/305\\\/social_img_156.jpg\",\"linkItems\":[],\"displayText\":\"The Ultimate Air Compressor Guide\"}]},{\"URL\":\"\\\/outdoor\\\/electric-generators-direct.html\",\"displayText\":\"Electric Generators\",\"sectionLinks\":{\"columns\":\"6\",\"linkItems\":[{\"URL\":\"\\\/power\\\/portable-generators.html\",\"imageURL\":\"\\\/nav-image\\\/100\\\/generator-13-1.jpg\",\"displayText\":\"Portable\"},{\"URL\":\"\\\/power\\\/home-standby-generators.html\",\"imageURL\":\"\\\/nav-image\\\/100\\\/generator-13-2.jpg\",\"displayText\":\"Home Standby\"},{\"URL\":\"\\\/power\\\/commercial-standby-generators.html\",\"imageURL\":\"\\\/nav-image\\\/100\\\/generator-13-3.jpg\",\"displayText\":\"Commercial\"},{\"URL\":\"\\\/power\\\/rv-generators.html\",\"imageURL\":\"\\\/nav-image\\\/100\\\/generator-13-4.jpg\",\"displayText\":\"RV\"},{\"URL\":\"\\\/power\\\/pto-generators.html\",\"imageURL\":\"\\\/nav-image\\\/100\\\/generator-13-5.jpg\",\"displayText\":\"PTO\"},{\"URL\":\"\\\/power\\\/transfer-switches.html\",\"imageURL\":\"\\\/nav-image\\\/100\\\/generator-13-6.jpg\",\"displayText\":\"Transfer Switches\"}]},\"subCategories\":[{\"URL\":null,\"type\":\"list\",\"title\":\"Featured Categories\",\"linkItems\":[{\"URL\":\"\\\/power\\\/whole-house-standby-generators.html\",\"displayText\":\"Whole House\"},{\"URL\":\"\\\/power\\\/inverter-generators.html\",\"displayText\":\"Inverter\"},{\"URL\":\"\\\/power\\\/electric-start-portable-generators.html\",\"displayText\":\"Electric Start\"},{\"URL\":\"\\\/power\\\/dual-fuel-generators.html\",\"displayText\":\"Dual Fuel\"},{\"URL\":\"\\\/power\\\/solar-generators.html\",\"displayText\":\"Solar Powered\"}]},{\"URL\":null,\"type\":\"list\",\"title\":\"Accessories\",\"linkItems\":[{\"URL\":\"\\\/power\\\/generator-power-cords.html\",\"displayText\":\"Power Cords\"},{\"URL\":\"\\\/power\\\/power-inlet-boxes.html\",\"displayText\":\"Power Inlet Boxes\"},{\"URL\":\"\\\/power\\\/generator-maintenance-kits.html\",\"displayText\":\"Maintenance Kits\"},{\"URL\":\"\\\/power\\\/portable-generator-covers.html\",\"displayText\":\"Covers & Tents\"},{\"URL\":\"\\\/outdoor\\\/electric-generator-accessories.html\",\"displayText\":\"All Accessories\"}]},{\"URL\":null,\"type\":\"list\",\"title\":\"Shop by Brand\",\"linkItems\":[{\"URL\":\"\\\/outdoor\\\/generac.html\",\"displayText\":\"Generac\"},{\"URL\":\"\\\/power\\\/honda-generators.html\",\"displayText\":\"Honda\"},{\"URL\":\"\\\/power\\\/kohler-generators.html\",\"displayText\":\"Kohler\"},{\"URL\":\"\\\/power\\\/briggs-and-stratton-generators.html\",\"displayText\":\"Briggs & Stratton\"},{\"URL\":\"\\\/power\\\/champion-generators.html\",\"displayText\":\"Champion\"}]},{\"URL\":\"\\\/stories\\\/305-How-to-Pick-the-Perfect-Electric-Generator.html\",\"type\":\"image\",\"title\":\"Buyer's Guide\",\"imageURL\":\"\\\/nav-article-image\\\/305\\\/social_img_305.jpg\",\"linkItems\":[],\"displayText\":\"What Kind of Generator do I Need for my House\"}]},{\"URL\":\"\\\/outdoor\\\/pressure-washers-direct.html\",\"displayText\":\"Pressure Washers\",\"sectionLinks\":{\"columns\":\"6\",\"linkItems\":[{\"URL\":\"\\\/power\\\/gas-pressure-washers.html\",\"imageURL\":\"\\\/nav-image\\\/100\\\/pressure-washer-13-1.jpg\",\"displayText\":\"Gas\"},{\"URL\":\"\\\/power\\\/electric-pressure-washers.html\",\"imageURL\":\"\\\/nav-image\\\/100\\\/pressure-washer-13-2.jpg\",\"displayText\":\"Electric\"},{\"URL\":\"\\\/power\\\/pressure-washer-pumps.html\",\"imageURL\":\"\\\/nav-image\\\/100\\\/pressure-washer-13-3.jpg\",\"displayText\":\"Pumps\"},{\"URL\":\"\\\/power\\\/pressure-washer-hoses.html\",\"imageURL\":\"\\\/nav-image\\\/100\\\/pressure-washer-13-4.jpg\",\"displayText\":\"Hoses\"},{\"URL\":\"\\\/power\\\/jetters.html\",\"imageURL\":\"\\\/nav-image\\\/100\\\/pressure-washer-13-5.jpg\",\"displayText\":\"Jetters\"},{\"URL\":\"\\\/power\\\/commercial-pressure-washers.html\",\"imageURL\":\"\\\/nav-image\\\/100\\\/pressure-washer-13-6.jpg\",\"displayText\":\"Commercial\"}]},\"subCategories\":[{\"URL\":null,\"type\":\"list\",\"title\":\"Featured Categories\",\"linkItems\":[{\"URL\":\"\\\/power\\\/commercial-start-your-own-business-kits.html\",\"displayText\":\"Business Kits\"},{\"URL\":\"\\\/power\\\/commercial-truck-mount-pressure-washers.html\",\"displayText\":\"Truck Mount\"},{\"URL\":\"\\\/power\\\/commercial-wall-mount-pressure-washers.html\",\"displayText\":\"Wall Mount\"},{\"URL\":\"\\\/power\\\/hot-water-pressure-washers.html\",\"displayText\":\"Hot Water\"},{\"URL\":\"\\\/power\\\/gas-pressure-washers.html\",\"displayText\":\"Gas Powered\"}]},{\"URL\":null,\"type\":\"list\",\"title\":\"Accessories\",\"linkItems\":[{\"URL\":\"\\\/power\\\/surface-cleaners.html\",\"displayText\":\"Surface Cleaners\"},{\"URL\":\"\\\/power\\\/pressure-washer-telescoping-wands.html\",\"displayText\":\"Telescoping Wands\"},{\"URL\":\"\\\/power\\\/pressure-washer-spray-rollers.html\",\"displayText\":\"Spray Guns\"},{\"URL\":\"\\\/power\\\/pressure-washer-soap-nozzles.html\",\"displayText\":\"Nozzles\"},{\"URL\":\"\\\/power\\\/pressure-washer-attachment.html\",\"displayText\":\"All Accessories\"}]},{\"URL\":null,\"type\":\"list\",\"title\":\"Shop by Brand\",\"linkItems\":[{\"URL\":\"\\\/power\\\/simpson-pressure-washers.html\",\"displayText\":\"Simpson\"},{\"URL\":\"\\\/power\\\/pressure-pro-pressure-washers.html\",\"displayText\":\"Pressure-Pro\"},{\"URL\":\"\\\/power\\\/be-pressure-washers.html\",\"displayText\":\"BE\"},{\"URL\":\"\\\/power\\\/general-pump-pressure-washers.html\",\"displayText\":\"General Pump\"},{\"URL\":\"\\\/power\\\/easy-kleen-pressure-washers.html\",\"displayText\":\"Easy-Kleen\"}]},{\"URL\":\"\\\/stories\\\/343-How-to-Pick-the-Perfect-Pressure-Washer.html\",\"type\":\"image\",\"title\":\"Buyer's Guide\",\"imageURL\":\"\\\/nav-article-image\\\/305\\\/social_img_343.jpg\",\"linkItems\":[],\"displayText\":\"Pressure Washer Buyer's Guide\"}]},{\"URL\":\"\\\/outdoor\\\/sump-pumps-direct.html\",\"displayText\":\"Sump Pumps\",\"sectionLinks\":{\"columns\":\"6\",\"linkItems\":[{\"URL\":\"\\\/pumps\\\/primary-sump-pumps.html\",\"imageURL\":\"\\\/nav-image\\\/100\\\/primary_56776234fd355c5a6971fc4fe3b1a559.jpg\",\"displayText\":\"Primary\"},{\"URL\":\"\\\/pumps\\\/combination-sump-pump-systems.html\",\"imageURL\":\"\\\/nav-image\\\/100\\\/Combination_d1accf365a102db5033f2a6f6bd37f98.jpg\",\"displayText\":\"Combination\"},{\"URL\":\"\\\/pumps\\\/battery-backup-sump-pumps.html\",\"imageURL\":\"\\\/nav-image\\\/100\\\/Battery Backup_57ed4885b879f30ee0134fc50cf51b8f.jpg\",\"displayText\":\"Battery Backup\"},{\"URL\":\"\\\/pumps\\\/sewage-pumps.html\",\"imageURL\":\"\\\/nav-image\\\/100\\\/Sewage_7c435fa06b22cee7de46cb44ef798ee7.jpg\",\"displayText\":\"Sewage\"},{\"URL\":\"\\\/pumps\\\/grinder-pumps.html\",\"imageURL\":\"\\\/nav-image\\\/100\\\/Grinder_74abf9c1c797dbdc6bdaedc569127969.jpg\",\"displayText\":\"Grinder\"},{\"URL\":\"\\\/pumps\\\/specialty-sump-pumps.html\",\"imageURL\":\"\\\/nav-image\\\/100\\\/Specialty_2e682b88db34300c4023504e9e23c845.jpg\",\"displayText\":\"Specialty\"}]},\"subCategories\":[{\"URL\":null,\"type\":\"list\",\"title\":\"Featured Categories\",\"linkItems\":[{\"URL\":\"\\\/pumps\\\/primary-submersible-sump-pumps.html\",\"displayText\":\"Primary Submersible\"},{\"URL\":\"\\\/pumps\\\/sewage-pump-systems.html\",\"displayText\":\"Sewage Systems\"},{\"URL\":\"\\\/pumps\\\/effluent-pumps.html\",\"displayText\":\"Effluent\"},{\"URL\":\"\\\/pumps\\\/laundry-drain-pump-systems.html\",\"displayText\":\"Drain\"},{\"URL\":\"\\\/pumps\\\/primary-pedestal-sump-pumps.html\",\"displayText\":\"Primary Pedestal\"}]},{\"URL\":null,\"type\":\"list\",\"title\":\"Accessories\",\"linkItems\":[{\"URL\":\"\\\/pumps\\\/sump-pump-batteries.html\",\"displayText\":\"Batteries\"},{\"URL\":\"\\\/pumps\\\/sump-pump-switches.html\",\"displayText\":\"Switches\"},{\"URL\":\"\\\/pumps\\\/sump-pump-and-sewage-pump-control-boxes.html\",\"displayText\":\"Control Boxes\"},{\"URL\":\"\\\/pumps\\\/auxiliary-power-systems.html\",\"displayText\":\"Auxiliary Power System\"},{\"URL\":\"\\\/pumps\\\/sump-pump-accessory.html\",\"displayText\":\"All Accessories\"}]},{\"URL\":null,\"type\":\"list\",\"title\":\"Shop by Brand\",\"linkItems\":[{\"URL\":\"\\\/pumps\\\/liberty-pumps.html\",\"displayText\":\"Liberty Pumps\"},{\"URL\":\"\\\/pumps\\\/zoeller-pumps.html\",\"displayText\":\"Zoeller\"},{\"URL\":\"\\\/pumps\\\/phcc-pro-series-pumps.html\",\"displayText\":\"Pro Series\"},{\"URL\":\"\\\/pumps\\\/bur-cam-pumps.html\",\"displayText\":\"Burcam\"},{\"URL\":\"\\\/pumps\\\/ion-pumps.html\",\"displayText\":\"iON Products\"}]},{\"URL\":\"\\\/stories\\\/784-Best-Selling-and-Top-Rated-Sump-Pumps.html\",\"type\":\"image\",\"title\":\"Buyer's Guide\",\"imageURL\":\"\\\/nav-article-image\\\/305\\\/social_img_784.jpg\",\"linkItems\":[],\"displayText\":\"The Best Sump Pumps of 2024\"}]},{\"URL\":\"\\\/outdoor\\\/water-pumps-direct.html\",\"displayText\":\"Water Pumps\",\"sectionLinks\":{\"columns\":\"6\",\"linkItems\":[{\"URL\":\"\\\/pumps\\\/electric-water-pumps.html\",\"imageURL\":\"\\\/nav-image\\\/100\\\/water-pump-13-1.jpg\",\"displayText\":\"Electric\"},{\"URL\":\"\\\/pumps\\\/gas-powered-water-pumps.html\",\"imageURL\":\"\\\/nav-image\\\/100\\\/water-pump-13-2.jpg\",\"displayText\":\"Gas\"},{\"URL\":\"\\\/pumps\\\/well-pumps.html\",\"imageURL\":\"\\\/nav-image\\\/100\\\/water-pump-13-3.jpg\",\"displayText\":\"Well\"},{\"URL\":\"\\\/pumps\\\/dewatering-pumps.html\",\"imageURL\":\"\\\/nav-image\\\/100\\\/water-pump-13-5.jpg\",\"displayText\":\"Dewatering\"},{\"URL\":\"\\\/pumps\\\/trash-pumps.html\",\"imageURL\":\"\\\/nav-image\\\/100\\\/water-pump-13-6.jpg\",\"displayText\":\"Trash\"},{\"URL\":\"\\\/pumps\\\/sprinkler-pumps.html\",\"imageURL\":\"\\\/nav-image\\\/100\\\/sprinkler_503ba4a09158d65372eb111aeb27c0b3.jpg\",\"displayText\":\"Sprinkler\"}]},\"subCategories\":[{\"URL\":null,\"type\":\"list\",\"title\":\"Featured Categories\",\"linkItems\":[{\"URL\":\"\\\/pumps\\\/utility-pumps.html\",\"displayText\":\"Utility\"},{\"URL\":\"\\\/pumps\\\/chemical-pumps.html\",\"displayText\":\"Chemical\"},{\"URL\":\"\\\/pumps\\\/transfer-pumps.html\",\"displayText\":\"Transfer\"},{\"URL\":\"\\\/pumps\\\/diesel-powered-pumps.html\",\"displayText\":\"Diesel\"},{\"URL\":\"\\\/pumps\\\/miscellaneous-power-types.html\",\"displayText\":\"Specialty Power\"}]},{\"URL\":null,\"type\":\"list\",\"title\":\"Accessories\",\"linkItems\":[{\"URL\":\"\\\/pumps\\\/water-pump-discharge-hoses.html\",\"displayText\":\"Hoses\"},{\"URL\":\"\\\/pumps\\\/well-pump-control-boxes.html\",\"displayText\":\"Control Boxes\"},{\"URL\":\"\\\/pumps\\\/float-switches.html\",\"displayText\":\"Switches\"},{\"URL\":\"\\\/pumps\\\/water-pump-quick-couplings.html\",\"displayText\":\"Quick Couplings\"},{\"URL\":\"\\\/pumps\\\/water-pump-accessory.html\",\"displayText\":\"All Accessories\"}]},{\"URL\":null,\"type\":\"list\",\"title\":\"Shop by Brand\",\"linkItems\":[{\"URL\":\"\\\/pumps\\\/honda-water-pumps.html\",\"displayText\":\"Honda\"},{\"URL\":\"\\\/pumps\\\/flotec-water-pumps.html\",\"displayText\":\"Flotec\"},{\"URL\":\"\\\/pumps\\\/multiquip-water-pumps.html\",\"displayText\":\"Multiquip\"},{\"URL\":\"\\\/pumps\\\/tsurumi-water-pumps.html\",\"displayText\":\"Tsurumi Pump\"},{\"URL\":\"\\\/pumps\\\/red-lion-water-pumps.html\",\"displayText\":\"Red Lion\"}]},{\"URL\":\"\\\/stories\\\/281-How-to-Pick-the-Perfect-Water-Pump.html\",\"type\":\"image\",\"title\":\"Buyer's Guide\",\"imageURL\":\"\\\/nav-article-image\\\/305\\\/social_img_281.jpg\",\"linkItems\":[],\"displayText\":\"Water Pump Buyer's Guide\"}]},{\"URL\":null,\"displayText\":\"More\",\"sectionLinks\":{\"columns\":\"6\",\"linkItems\":[{\"URL\":\"https:\\\/\\\/www.ecomfort.com\\\/cooling\\\/ductless-mini-split-systems.html\",\"imageURL\":\"\\\/nav-image\\\/100\\\/ls120hev2_99293_600_566a8b8447567d17e07268f4f6d958a4.jpg\",\"displayText\":\"Mini Splits\"},{\"URL\":\"https:\\\/\\\/www.ecomfort.com\\\/cooling\\\/room-air-conditioners.html\",\"imageURL\":\"\\\/nav-image\\\/100\\\/mass_140040_cd360daf61cd951f5221c80ff4941449.png\",\"displayText\":\"Room ACs and PTACs\"},{\"URL\":\"\\\/power\\\/jetters.html\",\"imageURL\":\"\\\/nav-image\\\/100\\\/JD4040HG_12827_600_72dcd6c01efe128e37c54c597bd42b59.jpg\",\"displayText\":\"Jetters\"},{\"URL\":\"\\\/outdoor\\\/paint-sprayers-direct.html\",\"imageURL\":\"\\\/nav-image\\\/100\\\/805-000_76239_1000_21900ab5e97ce4d1a242111121a10762_59ff9bc3ee387c5dd0131fb6cb89b426.jpg\",\"displayText\":\"Paint Sprayers\"}]},\"subCategories\":[{\"URL\":null,\"type\":\"list\",\"title\":\"Home Equipment\",\"linkItems\":[{\"URL\":\"https:\\\/\\\/www.ecomfort.com\\\/cooling\\\/central-air-conditioners.html\",\"displayText\":\"Air Conditioners\"},{\"URL\":\"https:\\\/\\\/www.ecomfort.com\\\/heating\\\/boilers.html\",\"displayText\":\"Boilers\"},{\"URL\":\"https:\\\/\\\/www.ecomfort.com\\\/heating\\\/furnaces.html\",\"displayText\":\"Furnaces\"},{\"URL\":\"https:\\\/\\\/www.ecomfort.com\\\/cooling\\\/ductless-mini-split-systems.html\",\"displayText\":\"Mini Splits\"},{\"URL\":\"https:\\\/\\\/www.ecomfort.com\\\/water-heaters\\\/water-heaters.html\",\"displayText\":\"Water Heaters\"}]},{\"URL\":null,\"type\":\"list\",\"title\":\"Home Appliances\",\"linkItems\":[{\"URL\":\"https:\\\/\\\/www.ecomfort.com\\\/cooling\\\/beverage-coolers.html\",\"displayText\":\"Beverage Coolers\"},{\"URL\":\"https:\\\/\\\/www.ecomfort.com\\\/appliances\\\/garbage-disposals.html\",\"displayText\":\"Garbage Disposals\"},{\"URL\":\"https:\\\/\\\/www.ecomfort.com\\\/cooling\\\/kegerators.html\",\"displayText\":\"Kegerators\"},{\"URL\":\"https:\\\/\\\/www.ecomfort.com\\\/cooling\\\/room-air-conditioners.html\",\"displayText\":\"Room Air Conditioners\"},{\"URL\":\"https:\\\/\\\/www.ecomfort.com\\\/cooling\\\/wine-coolers.html\",\"displayText\":\"Wine Coolers\"}]},{\"URL\":null,\"type\":\"list\",\"title\":\"Tools\",\"linkItems\":[{\"URL\":\"\\\/tools\\\/air-tools.html\",\"displayText\":\"Air Tools\"},{\"URL\":\"https:\\\/\\\/www.ecomfort.com\\\/cooling\\\/tools.html\",\"displayText\":\"HVAC Tools\"},{\"URL\":\"\\\/outdoor\\\/paint-sprayers-direct.html\",\"displayText\":\"Paint Sprayers\"}]},{\"URL\":null,\"type\":\"list\",\"title\":\"Commercial Equipment\",\"linkItems\":[{\"URL\":\"\\\/tools\\\/demolition-tools.html\",\"displayText\":\"Demolition Tools\"},{\"URL\":\"\\\/power\\\/jetters.html\",\"displayText\":\"Jetters\"},{\"URL\":\"\\\/power\\\/light-towers.html\",\"displayText\":\"Light Towers\"}]}]},{\"URL\":\"\\\/how-to-library.php\",\"displayText\":\"How-to-Library\",\"sectionLinks\":{\"columns\":\"6\",\"linkItems\":[{\"URL\":null,\"imageURL\":null,\"displayText\":\"\"}]},\"subCategories\":[]},{\"URL\":\"\\\/outdoor\\\/power-equipment-on-sale.html\",\"displayText\":\"Weekly Specials\",\"sectionLinks\":{\"columns\":\"6\",\"linkItems\":[{\"URL\":null,\"imageURL\":null,\"displayText\":\"\"}]},\"subCategories\":[]},{\"URL\":\"https:\\\/\\\/www.ecomfort.com\\\/\",\"displayText\":\"HVAC at eComfort.com\",\"sectionLinks\":{\"columns\":\"6\",\"linkItems\":[{\"URL\":null,\"imageURL\":null,\"displayText\":\"\"}]},\"subCategories\":[]}],\"USP\":[{\"id\":\"479\",\"URL\":\"\\\/stories\\\/479-How-To-Get-Free-Shipping-On-Power-Equipment.html\",\"className\":\"icon-nav-usp-shipping\",\"displayText\":\"Free Shipping\"},{\"id\":\"359\",\"URL\":\"\\\/stories\\\/359-Serious-Power-Equipment-Worth-Bragging-About.html\",\"className\":\"icon-nav-usp-reviews\",\"displayText\":\"Expert Recommendations\"},{\"id\":\"1261\",\"URL\":\"\\\/stories\\\/1261-Power-Equipment-Direct-Credit-Made-Simple.html\",\"className\":\"icon-nav-usp-financing\",\"displayText\":\"Financing\"},{\"id\":\"1991\",\"URL\":\"\\\/stories\\\/1991-New-Customer-Referral-Program.html\",\"className\":\"icon-referral\",\"displayText\":\"Customer Referral Program\"}]}","siteLinkJSON":"{\"Resources\":{\"How to Library\":{\"href\":\"how-to-library.php\",\"title\":\"Power Equipment Direct How-To Library\"},\"Product Reviews\":{\"href\":\"reviews.php\",\"title\":\"Customer Reviews on Power Equipment Direct Products\"},\"Recommendations\":{\"href\":\"stories\\\/359-Serious-Power-Equipment-Worth-Bragging-About.html\",\"title\":\"Product Recommendations\"},\"Weekly Specials\":{\"href\":\"outdoor\\\/power-equipment-on-sale.html\",\"title\":\"Weekly Power Equipment Direct Specials\"},\"Manuals\":{\"href\":\"stories\\\/399-How-to-Access-Old-Power-Equipment-Manuals.html\",\"title\":\"Manual Lookup\"},\"Service Centers\":{\"href\":\"stories\\\/414-How-to-Find-a-Service-Center-For-Your-Power-Equipment.html\",\"title\":\"Service Centers\"},\"Technical Support\":{\"href\":\"stories\\\/425-How-to-Find-Tech-Support-For-Your-Power-Equipment.html\",\"title\":\"Technical Support\"}},\"Account\":{\"My Account\":{\"href\":\"account.php\",\"title\":\"Login to My Account\"},\"Email Preferences\":{\"href\":\"https:\\\/\\\/www.powerequipmentdirect.com\\\/newsletter_removal.php\",\"title\":\"Email Preferences\"},\"Manufacturer Login\":{\"href\":\"https:\\\/\\\/www.powerequipmentdirect.com\\\/partnerships\\\/login.php\",\"title\":\"Manufacturer Login\"}},\"Customer Service\":{\"Help Center\":{\"href\":\"contact_us.php\",\"title\":\"Help Center\"},\"Return Policy\":{\"href\":\"returns.php\",\"title\":\"Return Policy\"},\"Shipping Policy\":{\"href\":\"stories\\\/515-How-to-Easily-Unload-Power-Equipment.html\",\"title\":\"Shipping Policy\"},\"Product Recalls\":{\"href\":\"stories\\\/1175-Product-Recalls-for-Power-Equipment.html\",\"title\":\"Product Recalls\"},\"Track Order\":{\"href\":\"ordertracking.php\",\"title\":\"Order Tracking\"},\"Accessibility\":{\"href\":\"stories\\\/1769-Our-Commitment-to-Accessibility.html\",\"title\":\"Accessibility\"},\"Do Not Sell or
Share My Personal Information\":{\"href\":\"https:\\\/\\\/ferguson.bigidprivacy.cloud\\\/consumer\\\/#\\\/dMf02ovZbN\\\/Form-NHWperWAaFNVIQK\",\"title\":\"Do Not Sell or Share My Personal Information\"}},\"About Us\":{\"Our Stores\":{\"href\":\"https:\\\/\\\/www.powerequipmentdirect.com\\\/our-stores.php\",\"title\":\"Power Equipment Direct's Stores\"},\"Our Story\":{\"href\":\"https:\\\/\\\/www.powerequipmentdirect.com\\\/stories\\\/1982-How-We-Make-Buying-Technical-Products-Simple.html\",\"title\":\"Power Equipment Direct's Story\"},\"Careers\":{\"href\":\"https:\\\/\\\/www.powerequipmentdirect.com\\\/stories\\\/1924-Job-Openings.html\",\"title\":\"Careers @ Power Equipment Direct\"},\"Newsroom\":{\"href\":\"newsreleases.php\",\"title\":\"Power Equipment Direct News Center\"}},\"Contact Us\":{\"phone\":\"800-710-7499\",\"hours\":[\"M-F: 8-5 CST\",\"Sat: Closed\",\"Sun: Closed\"]}}","storeLinkJSON":"{\"AC Wholesalers\":{\"href\":\"https:\\\/\\\/www.acwholesalers.com\",\"title\":\"AC Wholesalers\"},\"Air Compressors Direct\":{\"href\":\"https:\\\/\\\/www.aircompressorsdirect.com\",\"title\":\"Air Compressors Direct\"},\"eComfort\":{\"href\":\"https:\\\/\\\/www.ecomfort.com\",\"title\":\"eComfort\"},\"Electric Generators Direct\":{\"href\":\"https:\\\/\\\/www.electricgeneratorsdirect.com\",\"title\":\"Electric Generators Direct\"},\"Power Equipment Direct\":{\"href\":\"https:\\\/\\\/www.powerequipmentdirect.com\",\"title\":\"Power Equipment Direct\"},\"Pressure Washers Direct\":{\"href\":\"https:\\\/\\\/www.pressurewashersdirect.com\",\"title\":\"Pressure Washers Direct\"},\"Sump Pumps Direct\":{\"href\":\"https:\\\/\\\/www.sumppumpsdirect.com\",\"title\":\"Sump Pumps Direct\"},\"Water Pumps Direct\":{\"href\":\"https:\\\/\\\/www.waterpumpsdirect.com\",\"title\":\"Water Pumps Direct\"}}","socialLinkJSON":"{\"Facebook\":{\"href\":\"https:\\\/\\\/www.facebook.com\\\/PowerEquipmentDirect\",\"icon\":\"icon-facebook\",\"title\":\"Facebook\"},\"Twitter\":{\"href\":\"http:\\\/\\\/twitter.com\\\/PowerEquipment\",\"icon\":\"icon-twitter\",\"title\":\"Twitter\"},\"Pinterest\":{\"href\":\"http:\\\/\\\/pinterest.com\\\/powerequipment\\\/\",\"icon\":\"icon-pinterest\",\"title\":\"Pinterest\"},\"YouTube\":{\"href\":\"http:\\\/\\\/www.youtube.com\\\/PowerEquipmentDirect\",\"icon\":\"icon-youtube\",\"title\":\"YouTube\"},\"Instagram\":{\"href\":\"https:\\\/\\\/www.instagram.com\\\/powerequipmentdirect\\\/\",\"icon\":\"icon-instagram\",\"title\":\"Instagram\"},\"LinkedIn\":{\"href\":\"https:\\\/\\\/www.linkedin.com\\\/company\\\/power-equipment-direct\\\/about\\\/\",\"icon\":\"icon-linkedin\",\"title\":\"LinkedIn\"}}","miscLinkJSON":"{\"Terms of Use\":{\"href\":\"terms-of-use.php\",\"title\":\"Terms of Use\"},\"Privacy Policy & Security\":{\"href\":\"privacy.php\",\"title\":\"Privacy Policy and Security\"},\"Cookie Policy\":{\"href\":\"privacy.php#cookiePolicy\",\"title\":\"Cookie Policy\"},\"CA Privacy Rights\":{\"href\":\"privacy.php#californiaPrivacyRights\",\"title\":\"CA Privacy Rights\"},\"copyright\":\"© 2024 Power Equipment Direct. All Rights Reserved\"}","checkoutMiscLinkJSON":"{\"Privacy Policy & Security\":{\"href\":\"privacy.php\",\"title\":\"Privacy Policy and Security\"},\"Cookie Policy\":{\"href\":\"privacy.php#cookiePolicy\",\"title\":\"Cookie Policy\"},\"Terms of Use\":{\"href\":\"terms-of-use.php\",\"title\":\"Terms of Use\"},\"copyright\":\"© 2024 Power Equipment Direct. All Rights Reserved\"}","expertJSON":{"imageURL":"https:\/\/www.powerequipmentdirect.com\/images\/experts\/expert-main-13.png","href":"\/product-experts.php?s=13","title":"Contact Dale @ Power Equipment Direct","expertName":"Dale","expertTitle":"Power Equipment Expert"},"bbbJSON":{"imageURL":"https:\/\/www.powerequipmentdirect.com\/images\/badge-bbb.png","imageAlt":"Better Business Bureau\u00ae","href":"http:\/\/www.bbb.org\/chicago\/business-reviews\/industrial-equipment-and-supplies\/power-equipment-direct-in-bolingbrook-il-57001088","title":"Power Equipment Direct - A+ Rating - Better Business Bureau\u00ae"},"zipCode":null,"phoneNumber":"800-710-7499","loginToken":"page cache precludes the use of csrf tokens","iterable":"e4b27e68b9c84fbb940829a0a9ee29d7","newNav":false}
Share My Personal Information\":{\"href\":\"https:\\\/\\\/ferguson.bigidprivacy.cloud\\\/consumer\\\/#\\\/dMf02ovZbN\\\/Form-NHWperWAaFNVIQK\",\"title\":\"Do Not Sell or Share My Personal Information\"}},\"About Us\":{\"Our Stores\":{\"href\":\"https:\\\/\\\/www.powerequipmentdirect.com\\\/our-stores.php\",\"title\":\"Power Equipment Direct's Stores\"},\"Our Story\":{\"href\":\"https:\\\/\\\/www.powerequipmentdirect.com\\\/stories\\\/1982-How-We-Make-Buying-Technical-Products-Simple.html\",\"title\":\"Power Equipment Direct's Story\"},\"Careers\":{\"href\":\"https:\\\/\\\/www.powerequipmentdirect.com\\\/stories\\\/1924-Job-Openings.html\",\"title\":\"Careers @ Power Equipment Direct\"},\"Newsroom\":{\"href\":\"newsreleases.php\",\"title\":\"Power Equipment Direct News Center\"}},\"Contact Us\":{\"phone\":\"800-710-7499\",\"hours\":[\"M-F: 8-5 CST\",\"Sat: Closed\",\"Sun: Closed\"]}}","storeLinkJSON":"{\"AC Wholesalers\":{\"href\":\"https:\\\/\\\/www.acwholesalers.com\",\"title\":\"AC Wholesalers\"},\"Air Compressors Direct\":{\"href\":\"https:\\\/\\\/www.aircompressorsdirect.com\",\"title\":\"Air Compressors Direct\"},\"eComfort\":{\"href\":\"https:\\\/\\\/www.ecomfort.com\",\"title\":\"eComfort\"},\"Electric Generators Direct\":{\"href\":\"https:\\\/\\\/www.electricgeneratorsdirect.com\",\"title\":\"Electric Generators Direct\"},\"Power Equipment Direct\":{\"href\":\"https:\\\/\\\/www.powerequipmentdirect.com\",\"title\":\"Power Equipment Direct\"},\"Pressure Washers Direct\":{\"href\":\"https:\\\/\\\/www.pressurewashersdirect.com\",\"title\":\"Pressure Washers Direct\"},\"Sump Pumps Direct\":{\"href\":\"https:\\\/\\\/www.sumppumpsdirect.com\",\"title\":\"Sump Pumps Direct\"},\"Water Pumps Direct\":{\"href\":\"https:\\\/\\\/www.waterpumpsdirect.com\",\"title\":\"Water Pumps Direct\"}}","socialLinkJSON":"{\"Facebook\":{\"href\":\"https:\\\/\\\/www.facebook.com\\\/PowerEquipmentDirect\",\"icon\":\"icon-facebook\",\"title\":\"Facebook\"},\"Twitter\":{\"href\":\"http:\\\/\\\/twitter.com\\\/PowerEquipment\",\"icon\":\"icon-twitter\",\"title\":\"Twitter\"},\"Pinterest\":{\"href\":\"http:\\\/\\\/pinterest.com\\\/powerequipment\\\/\",\"icon\":\"icon-pinterest\",\"title\":\"Pinterest\"},\"YouTube\":{\"href\":\"http:\\\/\\\/www.youtube.com\\\/PowerEquipmentDirect\",\"icon\":\"icon-youtube\",\"title\":\"YouTube\"},\"Instagram\":{\"href\":\"https:\\\/\\\/www.instagram.com\\\/powerequipmentdirect\\\/\",\"icon\":\"icon-instagram\",\"title\":\"Instagram\"},\"LinkedIn\":{\"href\":\"https:\\\/\\\/www.linkedin.com\\\/company\\\/power-equipment-direct\\\/about\\\/\",\"icon\":\"icon-linkedin\",\"title\":\"LinkedIn\"}}","miscLinkJSON":"{\"Terms of Use\":{\"href\":\"terms-of-use.php\",\"title\":\"Terms of Use\"},\"Privacy Policy & Security\":{\"href\":\"privacy.php\",\"title\":\"Privacy Policy and Security\"},\"Cookie Policy\":{\"href\":\"privacy.php#cookiePolicy\",\"title\":\"Cookie Policy\"},\"CA Privacy Rights\":{\"href\":\"privacy.php#californiaPrivacyRights\",\"title\":\"CA Privacy Rights\"},\"copyright\":\"© 2024 Power Equipment Direct. All Rights Reserved\"}","checkoutMiscLinkJSON":"{\"Privacy Policy & Security\":{\"href\":\"privacy.php\",\"title\":\"Privacy Policy and Security\"},\"Cookie Policy\":{\"href\":\"privacy.php#cookiePolicy\",\"title\":\"Cookie Policy\"},\"Terms of Use\":{\"href\":\"terms-of-use.php\",\"title\":\"Terms of Use\"},\"copyright\":\"© 2024 Power Equipment Direct. All Rights Reserved\"}","expertJSON":{"imageURL":"https:\/\/www.powerequipmentdirect.com\/images\/experts\/expert-main-13.png","href":"\/product-experts.php?s=13","title":"Contact Dale @ Power Equipment Direct","expertName":"Dale","expertTitle":"Power Equipment Expert"},"bbbJSON":{"imageURL":"https:\/\/www.powerequipmentdirect.com\/images\/badge-bbb.png","imageAlt":"Better Business Bureau\u00ae","href":"http:\/\/www.bbb.org\/chicago\/business-reviews\/industrial-equipment-and-supplies\/power-equipment-direct-in-bolingbrook-il-57001088","title":"Power Equipment Direct - A+ Rating - Better Business Bureau\u00ae"},"zipCode":null,"phoneNumber":"800-710-7499","loginToken":"page cache precludes the use of csrf tokens","iterable":"e4b27e68b9c84fbb940829a0a9ee29d7","newNav":false}
We Make Buying Technical Products Simple